WAREHOUSE CLEANING SERVICES
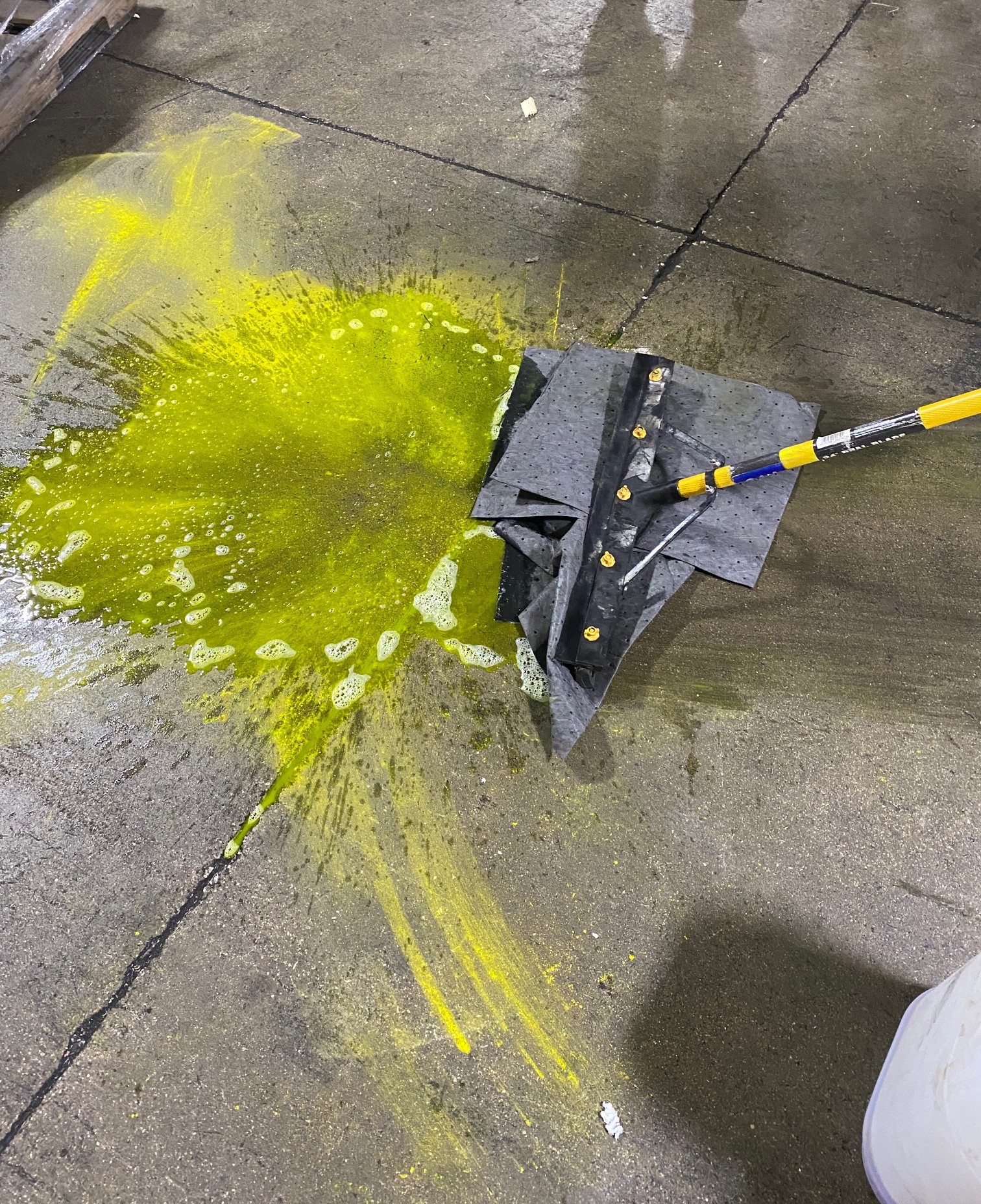
If it can tip or spill, it probably will! Warehouses across the nation commonly store hazardous materials to varying degrees. From gas cylinders to liquid paints and chemicals, these facilities are frequent locations for HAZMAT incidents. According to the United States Agency for Toxic Substances and Disease Registry (ATSDR), approximately 75% of HAZMAT emergencies take place in storage facilities. Among these occurrences, 36% involve the storage of incompatible chemicals, and 22% happen due to improper storage equipment usage. Warehouses accidents where hazardous materials are present can pose significant risks to occupants. Swiftly engaging the expertise of HAZMAT-trained warehouse cleaning services company such as HazChem Environmental, is crucial for warehouse sanitation and for overall warehouse safety. Implementing industrial warehouse cleaning practices enhances safety and mitigates the chances of accidents. To ensure warehouse safety, the OSHA Warehousing Safety Checklist proves to be an invaluable resource.
Hazardous Material Spill Prevention and Preparation
In line with the guidelines of the Workplace Hazardous Materials Information System (WHMIS), it’s crucial to acknowledge the potential for spills or leaks when chemicals are utilized within a workplace environment. The critical aspect lies in the readiness of a effective spill cleanup plan. Equipping oneself with the necessary tools and gear significantly contributes to averting spills that could jeopardize the well-being and livelihoods of employees.
Prior to delving into spill cleanup procedures, nearly as imperative is the endeavor to prevent spills from occurring in the first place. It’s imperative to assess areas where equipment in the workplace could potentially leak; these are key areas to inspect:
-
- Hydraulic lines
- Pipes, hoses, or any conduits carrying fluids
- Fluid-holding containers warrant scrutiny for signs of rust, bulging, or seams that might be giving way.
- Thoroughly assess fluid-holding containers that have been recently moved or transported, ensuring they haven’t incurred damage in transit.
Additional measures to preempt spills encompass the utilization of contoured or molded pallets to mitigate the risk of containers toppling over. Furthermore:
-
- Verify that liquid containers aren’t positioned too close to the edge of shelving.
- Containers should ideally be stored with their openings facing upward.
- Contemplate the installation of seep-through floor mats around fluid-holding containers; these will channel any spillage beneath the walking surface, consequently reducing the potential for slip and fall accidents.
Another layer of prevention lies in maintaining a clean and clutter-free work environment. Tidiness and regular maintenance of workplaces naturally foster a culture of safety, and reduces warehouse accidents; employees tend to exhibit greater regard for the facility, their personal safety, and the safety of their colleagues within such an environment.
Be Prepared for a Potential Warehouse Spill or Forklift Accident
- Acquire and have available appropriate employee attire to ensure the safe handling of hazardous materials: Equipping your employees with personal protective equipment (PPE) is crucial to their safety while dealing with hazardous substances. At a minimum, workers should have gloves, eye protection, and boots. While full hazmat suits are rarely necessary in most warehouse scenarios, it’s highly recommended to provide proper coveralls. When handling corrosive materials, using face shields is also advised.
- Implement signage and visual aids: Maintain a comprehensive range of visual aids such as preventative floor signs, floor safety tape, tool shadow tape, and aisle markings.
- Install spill containment solutions: Take proactive measures by installing spill pallets underneath liquid storage containers to prevent leaks and spills. The appropriate size of the spill pallet depends on the container size. For drums holding 55 gallons or more, a spill pallet with complete coverage is essential to effectively catch spills from all sides. It’s essential that the spill pallet is designed to hold at least 35% of the drum’s content.
In addition to these preventive steps, there are also recommended protocols to adhere to when addressing a spill. These encompass refraining from direct contact with the spilled substance, using absorbent materials to contain it, investigating the root cause of the spill, and ultimately strategizing ways to avert its recurrence. For more comprehensive guides on appropriate spill response procedures, you can refer to the resources available on the United States Department of Labor website or reach out to HazChem Environmental for assistance, available round the clock.
What To Do if There is a Forklift Accident or Warehouse Spill:
Hazardous substances like chemicals are prevalent in virtually all workplaces, ranging from flammable cleaning agents and lubricants to corrosive compounds utilized in manufacturing. These substances can be toxic or flammable, posing risks to both workers and the environment.
To prevent chemical spills, it is crucial to establish comprehensive industrial warehouse cleaning rules that encompass the proper handling, storage, usage, and disposal of these hazardous materials. All employees must be capable of identifying potential hazards and understanding how to manage them. Despite stringent safety protocols and training, warehouse accidents, including spills, can occur unexpectedly.
Guidelines to Ensure Readiness for Spill Incidents:
-
- Have A Plan: The Environmental Protection Agency mandates the existence of written plans for addressing emergencies, including spills. Having a predefined action plan is essential for safeguarding workers and minimizing environmental damage. All employees should be aware of spill response procedures, even if it’s simply knowing the evacuation route. Rigorous planning, training, and simulations are vital to ensure preparedness for spill scenarios. The plan should encompass material safety data sheets (MSDSs) for workplace chemicals, spill response steps, utilization of personal protective equipment (PPE), emergency cleanup company contact information for spill incidents, evacuation protocols, and procedures for containment, cleanup, decontamination, and proper disposal of spilled materials.
- Training: Occupational Safety and Health Administration (OSHA) guidelines stipulate that employees receive training on handling workplace hazards. Since each spill situation is unique, workers must comprehend the risks associated with different types of spills and how to respond safely. For instance, handling a spill in a production area may vary from addressing one on a loading dock. Here’s a general outline for addressing spills in various workplace settings:
- Identify the Spilled Substance: Recognize liquids leaking from labeled containers. For unidentified spills, employees should refrain from attempting to identify the material. Contact individuals within the spill response plan who can accurately identify the substance and seek assistance from professionals like HazChem Environmental.
- Report the Spill: Regardless of identification, employees need to know where and how to report spills. Responsible parties might have to report spills to external agencies as well, depending on the situation and regulatory requirements. Have HazChem’s number readily available and posted.
- Protect Responders: Responding personnel should be aware of required PPE. In cases where the spilled substance remains unknown, responders should assume the worst and use all available PPE, including gloves, boots, goggles, breathing apparatus, monitors, and detectors. Maintain essential tools alongside PPE and inspect them regularly for readiness.
- Ensure Life Safety: Prioritize safety during spill responses. If injuries or contamination are evident, promptly call emergency services. Trained responders should provide initial assistance until professional help arrives. Conduct regular drills to ensure familiarity with procedures, especially considering the challenges posed by wearing PPE.
- Contain the Spill: After attending to any injured individuals, contain the spill to prevent further spread. Placing barriers (dikes) around the spill area and covering nearby drains help contain hazardous materials and prevent their entry into drainage systems.
- Address the Source: If the spill continues, take steps to stop it. This might involve shutting off valves, patching leaks, or repositioning containers to stop leaks.
- Warehouse Clean Up: Begin warehouse cleanup once injured individuals are safe and the source of the spill is contained. Start from the outer edges and work inward to ensure thorough cleaning. Various absorbent materials, such as mops, towels, mats, and socks, can be utilized, along with shop vacuums for larger spills. Collaborating with local HAZMAT teams during training drills enhances familiarity with warehouse layouts and spill response procedures.
- Decontamination: After spill containment and cleanup, establish a decontamination area for responders before leaving the spill zone. Injured individuals must undergo decontamination before medical treatment. Thoroughly clean the entire area, as well as tools and equipment used during cleanup.
- Documentation: Familiarize yourself with applicable warehouse sanitation regulations. Depending on spill characteristics, reports may need to be submitted to local, state, or federal agencies. This is also an opportunity to evaluate the response and identify areas for improvement. Adjusting the emergency plan enhances future spill responses.
- Replenish Supplies: Create an inventory and restock all supplies and PPE utilized during cleanup promptly to ensure preparedness for future spill incidents.
Hazardous Material Safety: Let Hazchem assist to help keep you Safe & Compliant
Operate a warehouse that stores hazardous material safely and take the necessary precautions such as:
- Properly reading the MSDS documentation when goods arrive
- Organizing the material and properly storing it
- Frequently inspecting the hazardous material for damages or any observable issues
- Supply warehouse workers with proper PPE and training to handle the material in case of a spill
For more information refer to the Codes and Standards below:
Hazards can result in both short and long-term consequences. There are two distinct categories of hazards: those related to physical factors and those impacting health (see below). Safety measures and protocols are in place to minimize the occurrence of such incidents, including the application of labels, regular goods inspections, efficient storage practices, and various other effective safety strategies. We will explore diverse approaches for safeguarding warehouse personnel against potential hazards, along with preventive actions that can be instituted across the warehouse to increase warehouse safety.
Physical: Fire, corrosion, and reactions with other substances may be caused by some materials.
Health: Acute toxicity, skin irritation, respiratory discomfort, eye damage, and prolonged carcinogenic effects are health hazards from some materials.
Unsafe Substances and Materials Need Proper Labelling
Labels offer the simplest means of recognizing potential hazards that may be encountered. Utilizing accurate labels serves a dual purpose: it facilitates the identification of various substances entering the warehouse and aids in their segregation and arrangement. The proper labels help to identify hazardous materials throughout North America.
The “Hazard Diamond” (shown below) from the National Fire Protection Association (NFPA 704)
Label usage helps workers to separate hazardous substances. It is also important to keep incompatible materials at a safe distance from each other such as:
- Acid + Bases
- Flammables + Oxidizers
- Water Reactive + Aqueous Solutions
Storage of Dangerous Hazardous Materials is Key
Maintaining an orderly warehouse equipped with labeled products and designated zones significantly streamlines the storage process for hazardous substances, increasing warehouse safety. Moreover, there are crucial protocols to enhance warehouse safety concerning hazardous materials. These include:
- Establishing a well-organized receiving area equipped with comprehensive information and documentation for each received substance, facilitating accurate identification of incoming and outgoing items.
- Ensuring that every received material is accompanied by a Material Safety Data Sheet (MSDS) containing essential details such as product information, hazardous ingredients, physical characteristics, fire and explosion risks, reactivity properties, toxicological attributes, preventative measures, first-aid procedures, and preparation information.
- Thoroughly inspecting received goods for any signs of damage, such as punctures, leaks, or other forms of impairment that could heighten spill risks.
- Properly ventilating storage areas for hazardous substances while maintaining a considerable distance from heat sources and direct sunlight.
- Utilizing construction materials that are resistant to chemicals throughout the facility.
- Employing containers, cabinets, and refrigeration units that are approved for chemical use.
- Arranging stored materials based on their chemical compatibility, rather than relying solely on alphabetical organization.
- Ensuring that the ventilation systems (both supply and exhaust) adhere to ASHRAE Standards 62.1 and 62.2 for hazardous materials.
- Verifying that the sprinkler system (whether water-based or foam-based) complies with the NFPA Chapter 16 and 17 regulations for hazardous materials.
SUPER-FAST 60-Minute Response Time
We understand the urgent and critical nature of your call for service. Our Emergency Rapid Response Teams are ready, willing and able to respond quickly to remedy your emergency spill situation. Our Emergency Response Vehicles are pre-loaded with 90% of the equipment needed for any emergency situation. The final 10% will be added for your particular needs. This advance preparation enables us to deploy a Team within 60 minutes or less from our facility. Based upon our clients’ feedback, this is far better than the typical response time from most of our competitors. Their response is usually measured in multiple hours, and sometimes days or even weeks. Our Team is always ready to deploy, 24 hours a day, 365 days per year, rain or shine, including holidays. We do not rely on automated answering systems for our main phone line (630) 458-1910. Instead, we guarantee that a live person will answer your call, regardless of whether it is a weekend, holiday, or any other day.
Compliant. Responsive. Safe.
Call 630-458-1910 for immediate assistance. Open 24/7/365
For a FREE, no-obligation quote, click the button below